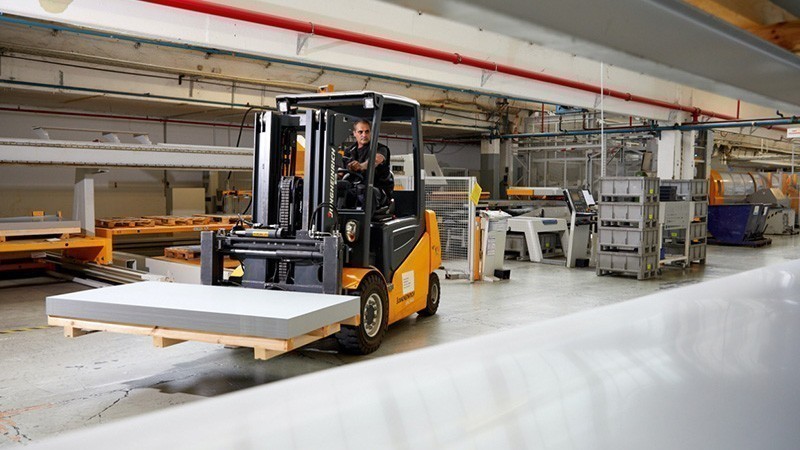
Short delivery times
We are happy to still enable fast and professional delivery of steel laboratory solutions – the performance remains high even in the challenging situation of COVID-19.
The demand for laboratory services – which has been rising for a long time – is currently reaching a peak. Laboratory capacities are limited by existing facilities. We are able to supply laboratory components which are tailored to the current demanding requirements within 4-5 weeks*. Technical details need to be clarified as quickly as possible so that in-house planning can implement the specifications precisely. Quality and safety are the top priorities of the tailor-made steel furnishing components and systems. The material supports the hygienic requirements of laboratory environments to a considerable extent, and is resistant, durable and recyclable. Especially in these challenging times, laboratory equipment must not only be functional, but also offer and support a maximum of safety. For more information don’t hesitate to get in touch via contact form on our website or phone.
* The 4-5 weeks delivery time guarantee applies from the time when all commercial and technical questions have been resolved and measurement and drawings have been approved, to the time of loading in Hänigsen (Germany). Specific wastewater and neutralisation systems, special worktop systems and specific gas applications are excluded from this guarantee due to their complexity. Here we coordinate individually with you regarding the shortest possible delivery time